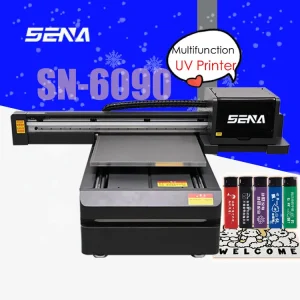
1. The Importance of a Suitable Working Environment
When it comes to operating an English – version UV printer, the working environment is of utmost significance. A proper working environment is the cornerstone for ensuring the stable operation of the UV printer, high – quality printing results, and an extended lifespan of the equipment.
For the stable operation of the printer, an inappropriate environment can cause various malfunctions. For example, if the working area has excessive dust, the dust particles may infiltrate into the internal components of the printer, such as the mechanical moving parts like the guide rails and belts. This can lead to increased friction, making the movement of the print head unsmooth, and even cause jams during the printing process. In severe cases, it may damage the motor driving these components, resulting in costly repairs or replacements.
Print quality is highly dependent on the working environment as well. Temperature and humidity play crucial roles. If the temperature is too high, the UV ink may dry too quickly, leading to inconsistent ink droplet deposition on the printing material. This can cause uneven color distribution, streaks in the printed image, and a decrease in the overall sharpness of the graphics. On the contrary, if the temperature is too low, the ink may become too viscous, which makes it difficult for the print head to eject the ink smoothly, also resulting in poor – quality prints. Humidity also affects the printing process. High humidity can cause the printed material to absorb moisture, which may lead to warping or swelling. This, in turn, will cause the printed image to be distorted. For instance, when printing on paper – based materials in a high – humidity environment, the paper may wrinkle, and the ink may bleed, ruining the print quality.
The lifespan of the UV printer is also directly related to the working environment. A corrosive environment, such as one with high humidity or exposure to certain chemicals, can cause the metal parts of the printer to rust. Components like the chassis, brackets, and some internal connectors are vulnerable to corrosion. Once corroded, their structural integrity is compromised, which can lead to the misalignment of components and eventually shorten the lifespan of the entire printer. Additionally, if the printer is frequently exposed to extreme temperature changes, the thermal expansion and contraction of different parts can cause stress on the joints and connections, gradually weakening the mechanical and electrical connections inside the printer.
2. Temperature Requirements
2.1 Optimal Temperature Range
The optimal working temperature range for an English – version UV printer is typically between 18℃ – 30℃ (64°F – 86°F). This temperature range is crucial for maintaining the proper physical properties of the UV ink and ensuring the normal operation of the printer’s internal components.
When the temperature is within this range, the UV ink has the right viscosity. The ink can flow smoothly from the ink cartridges to the print head and then be accurately ejected onto the printing material. For example, in a printing workshop where the temperature is maintained at around 25℃, the inkjet process is stable, and the printed patterns have clear edges and accurate color reproduction. This is because at this temperature, the ink particles can be evenly distributed, and the curing reaction under the action of UV light can also proceed smoothly.
The printer’s electronic components also perform best within this temperature range. High – temperature – sensitive components such as integrated circuits and control boards can maintain normal electrical performance. They can accurately control the movement of the print head, the amount of ink ejection, and the operation of the UV curing lamp, ensuring the overall stability of the printing process.
2.2 Adjustment in Extreme Temperatures
In winter, when the temperature drops below the optimal range, the ink in the UV printer becomes thicker. This increased viscosity makes it difficult for the ink to flow freely through the ink channels and be ejected from the print head nozzles. As a result, the nozzles are prone to clogging. For instance, if the temperature in the workshop drops to 10℃, the ink may become so thick that the print head can no longer eject it evenly, leading to streaks or gaps in the printed image. To address this issue, it is necessary to pre – heat the printer before starting work. Many modern UV printers are equipped with pre – heating functions. You can turn on the printer in advance and let it run through a pre – heating cycle, which warms up the ink and the print head to a suitable temperature, ensuring smooth ink flow.
In summer, when the temperature is too high, problems such as ink splashing from the print head (also known as “flying ink”) may occur. The high temperature causes the ink to evaporate too quickly near the print head, and the ink droplets may be affected by the hot air flow, deviating from their normal trajectories. Additionally, the control board card of the printer is also at risk of overheating. High – temperature environments can cause the components on the control board to age rapidly and may even lead to malfunctions. To cool down the printer in high – temperature environments, air – conditioning equipment can be installed in the printing workshop to maintain a suitable indoor temperature. For larger workshops, industrial air conditioners or cooling units can be used. Another option is to install fans near the printer to enhance air circulation and help dissipate heat.
3.1 Ideal Humidity Level
The ideal humidity level for an English – version UV printer is between 30% – 70% (with no condensation). Humidity has a significant impact on the printing process. It affects the drying speed and viscosity of the ink, which in turn influences the print quality.
When the humidity is within the optimal range, the ink dries at an appropriate rate. In a 50% humidity environment, for example, the evaporation rate of the ink solvent is balanced. This allows the ink to solidify properly under UV light curing, resulting in a clear and sharp printed image. The viscosity of the ink also remains stable, ensuring that the ink can be evenly ejected from the print head. This leads to consistent ink droplet size and distribution, contributing to high – quality prints with accurate color reproduction and smooth transitions between colors.
3.2 Coping with High and Low Humidity
In low – humidity environments, usually below 30%, the ink in the UV printer dries too quickly. This can cause problems such as the formation of dry ink particles on the print head nozzles, which may lead to nozzle clogging. Once the nozzles are clogged, the ink ejection becomes irregular, resulting in missing dots or lines in the printed image. To solve this problem, a humidifier can be placed in the printing workshop. Ultrasonic humidifiers are a good choice as they can quickly increase the humidity in the air by releasing fine water droplets. Additionally, some printers are equipped with ink – circulation systems that can keep the ink in the print head flowing, reducing the risk of ink drying in the nozzles.
In high – humidity environments, typically above 70%, the ink can become overly viscous. This makes it difficult for the print head to eject the ink precisely, leading to blurred or smudged prints. Moreover, high humidity can cause paper – based printing materials to absorb moisture and wrinkle. When printing on wrinkled paper, the ink distribution becomes uneven, and the print quality deteriorates significantly. To address high – humidity issues, a dehumidifier can be used to remove excess moisture from the air. Desiccant – based dehumidifiers or refrigerant dehumidifiers are commonly used in printing workshops. Storing the printing materials in a dry place and using them as soon as possible after opening the packaging can also help prevent the materials from being affected by high humidity.
4. Cleanliness and Ventilation
4.1 The Need for a Clean Environment
A clean and low – dust working environment is crucial for an English – version UV printer. The print head of a UV printer is a highly precise component. Even the smallest dust particles can cause significant problems. When dust enters the print head, it can mix with the UV ink. This mixture can then block the tiny nozzles through which the ink is ejected. Once the nozzles are clogged, the ink flow becomes irregular. For example, instead of a continuous and even stream of ink droplets being ejected to form a smooth printed line, there may be gaps or inconsistent dot patterns. This leads to a loss of print quality, with the printed text or images appearing blurry, having missing parts, or showing uneven color density.
Moreover, dust can also scratch the delicate surface of the print head. As the print head moves back and forth during the printing process, dust particles trapped on its surface can act like abrasives, gradually wearing down the nozzle plates and other parts of the print head. This not only reduces the lifespan of the print head but also degrades the printing accuracy over time. To maintain a clean environment, the printing workshop should be regularly cleaned. Floors should be swept and mopped, and surfaces should be wiped down with dust – free cloths. Air – filtering systems can also be installed to reduce the amount of airborne dust in the workshop.
4.2 Importance of Good Ventilation
Good ventilation in the working area of the UV printer is essential. During the printing process, the UV ink and the UV curing lamp can produce various harmful substances. The UV ink contains volatile organic compounds (VOCs). When the ink is in use, these VOCs are released into the air. In a poorly ventilated environment, the concentration of these VOCs can build up. If operators are exposed to high levels of VOCs for an extended period, it can cause a range of health problems, including respiratory irritation, headaches, dizziness, and in severe cases, damage to the nervous system.
The UV curing lamp, on the other hand, can produce ozone. Ozone is a highly reactive gas. When present in high concentrations, it can irritate the respiratory tract, causing coughing, shortness of breath, and chest pain. Adequate ventilation helps to expel these harmful gases, maintaining a healthy working environment for the operators. Ventilation systems can be designed in different ways. For small – scale printing setups, simple exhaust fans can be installed near the printer to draw out the polluted air. In larger industrial printing facilities, more comprehensive ventilation systems, such as forced – air ventilation with air – handling units, can be used. These systems can not only remove the harmful gases but also regulate the temperature and humidity in the workshop to some extent, further contributing to the optimal operation of the UV printer.
5. Other Environmental Considerations
5.1 Lighting Conditions
The UV printer should be placed in an environment with low light. This is because the UV ink used in the printer is sensitive to light, especially ultraviolet light. Prolonged exposure to strong light sources, such as direct sunlight or high – intensity artificial ultraviolet lamps, can cause premature curing of the ink in the ink cartridges or in the print head nozzles. If the ink cures prematurely in the nozzles, it will block the ink – ejection channels, leading to problems such as inconsistent ink flow, missing dots in the printed image, and ultimately, a significant decline in print quality. Additionally, excessive light can also affect the performance of some of the printer’s optical components. For example, the sensors that detect the position of the print head and the movement of the printing platform may be interfered with by strong light, causing inaccurate positioning and affecting the precision of the printing process.
5.2 Placement and Stability
The UV printer must be placed on a flat and stable surface. An uneven surface can cause the printer to tilt slightly. This tilt can affect the movement of the print head during the printing process. The print head may not move in a completely horizontal or vertical direction as designed, resulting in uneven ink deposition on the printing material. For example, if the printer is placed on a surface that is sloping by just a few degrees, the printed lines may appear wavy, and the alignment of multi – color prints may be off, leading to color misregistration.
It is important to keep the front cover of the printer closed during operation. This helps to prevent dust from entering the internal components of the printer. The interior of the printer contains many sensitive components, such as the print head, ink – supply system, and mechanical moving parts. Once dust enters, it can accumulate on these components, causing problems like nozzle clogging, increased friction in moving parts, and electrical short – circuits in the control board.
Placing any objects on the body of the UV printer is strictly prohibited. Objects placed on the printer can add unnecessary weight and stress to the structure. This can potentially cause deformation of the printer’s chassis or affect the normal operation of the internal components. For example, if a heavy object is placed on the printer’s cover, it may cause the cover to warp, which can disrupt the proper sealing of the printer and allow more dust to enter.
When moving the UV printer, it is necessary to first disconnect all external power cords and data cables. This is to prevent damage to the electrical connectors and internal circuits due to sudden pulling or tugging during the moving process. After disconnecting the cables, it is advisable to mark or label them to ensure easy re – connection later. During the actual movement, avoid pushing or pulling the printer by its sensitive parts, such as the print head carriage or the UV curing lamp assembly. Instead, hold the main body of the printer firmly and move it slowly and steadily to the new location. If the printer is too heavy to move manually, appropriate lifting and moving equipment should be used to ensure the safety of the equipment and the people involved in the moving process.
In conclusion, maintaining the optimal working environment for an English – version UV printer is essential. The temperature should be kept between 18℃ – 30℃, and the humidity between 30% – 70% to ensure the proper flow and curing of the ink and the normal operation of components. A clean environment free of dust is crucial to prevent nozzle clogging and damage to the print head, while good ventilation is necessary to expel harmful substances generated during the printing process.
Low – light conditions are required to avoid premature ink curing, and the printer should be placed on a flat and stable surface, with the front cover closed during operation and no objects placed on its body. When moving the printer, proper precautions such as disconnecting cables should be taken.
Readers are urged to pay close attention to these environmental factors. By doing so, not only can the stable operation of the UV printer be guaranteed, but also high – quality printing results can be achieved, which is beneficial for improving work efficiency and reducing equipment maintenance costs. Whether you are a professional printer operator or a business owner using UV printers for production, creating a suitable working environment is the first step towards successful printing operations.